Installation & Connections of MSST5/10-S step motor drive
1. Connecting the power supply
The MSST5-S accepts a DC supply voltage from 24 to 48VDC. The MSST10-S accepts a DC supply voltage from 24 to 80VDC. Using the connector supplied and AWG 16 or 18 wire, connect to the power supply as in the diagram below.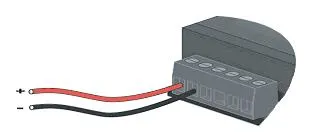

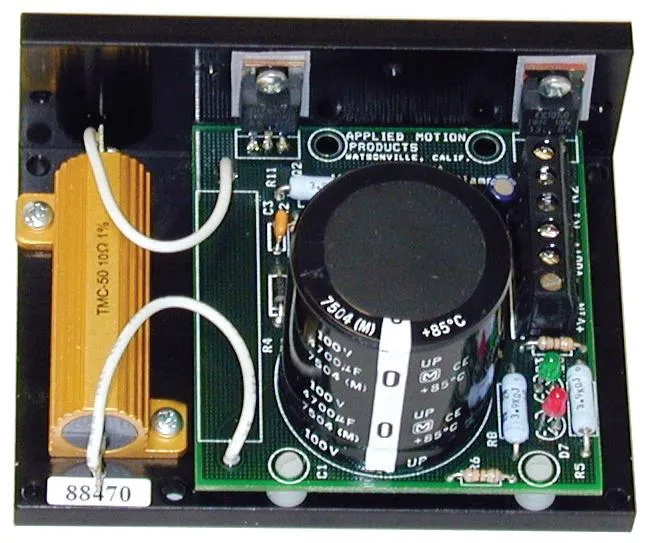
2. Connecting the Motor
Never connect the motor to or disconnect it from the drive. Insulate unused motor leads separately, and then secure them. Never connect motor leads to the ground or a power supply. There are several options for connecting a motor to a drive. Four lead motors can only be connected one way, as in the drawing below: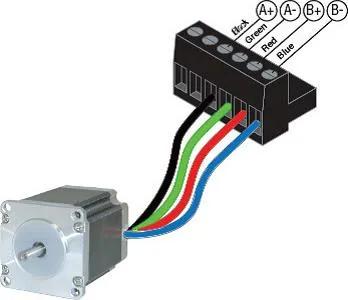
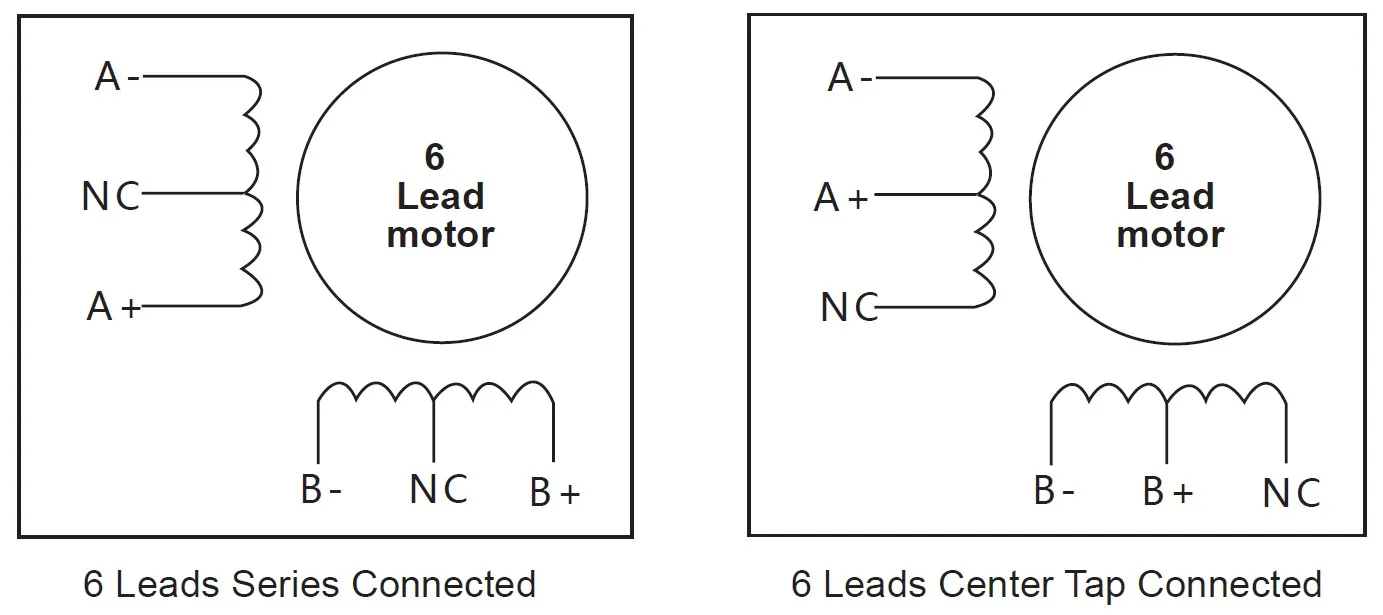
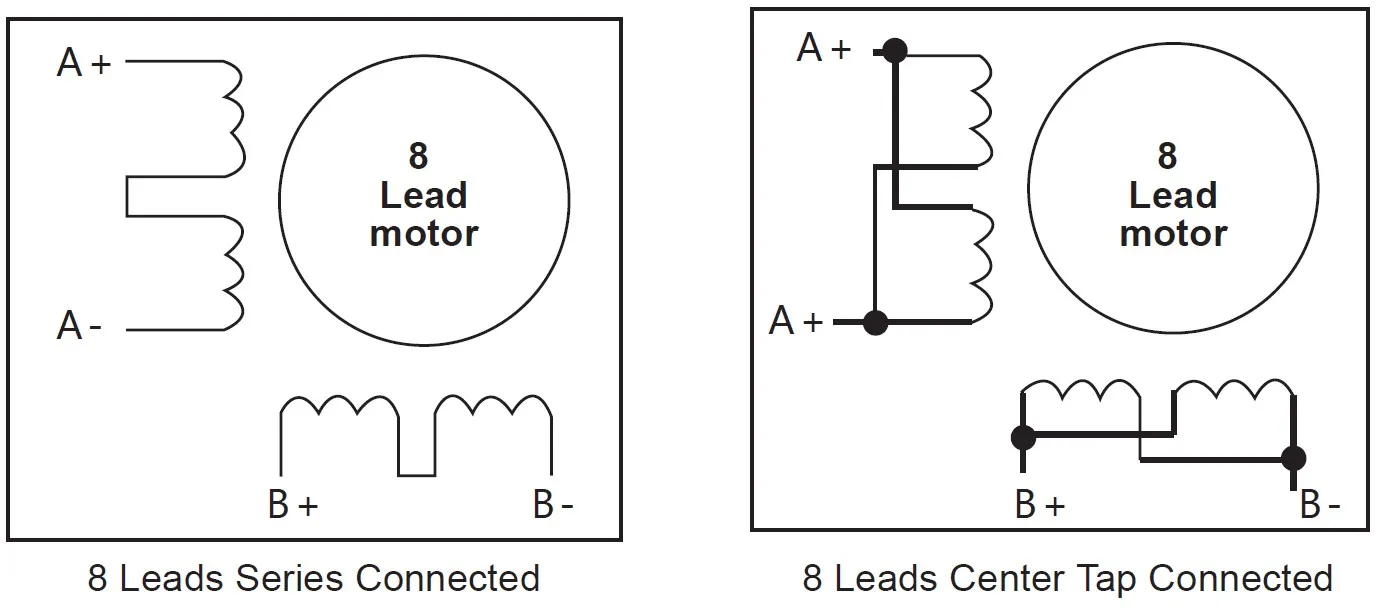
3. Connecting to the PC using RS-232
Locate your computer within 6 feet of the stepping driver. A black adapter plug was included with your driver. There is a telephone-style jack on one end and a larger 9-pin connector on the other end. Plug the large end into the COM1 serial port of your PC. Secure the adapter with the screws on the sides. If your PC's COM1 port is already in use by another program, you may be able to use the COM2 port for the stepping driver. On some PCs, COM2 has a 25-pin connector that does not fit the black adapter plug. If this is the case, and you must use COM2, you may need to purchase a 25 to 9-pin serial adapter from your local computer store. There is also the option of using the USB port on your computer via a USB to RS232 adapter available on the market as an alternative to using the COM serial port.4. Connecting the inputs and outputs
Pluggable, screw terminal connectors are used to connect the inputs and outputs. The three inputs (STEP, DIR, EN) are on the six-position connector. There are analog inputs and digital outputs on the five-position connector, along with 5VDC and a ground for analog connections.4.1 Connecting Digital Inputs
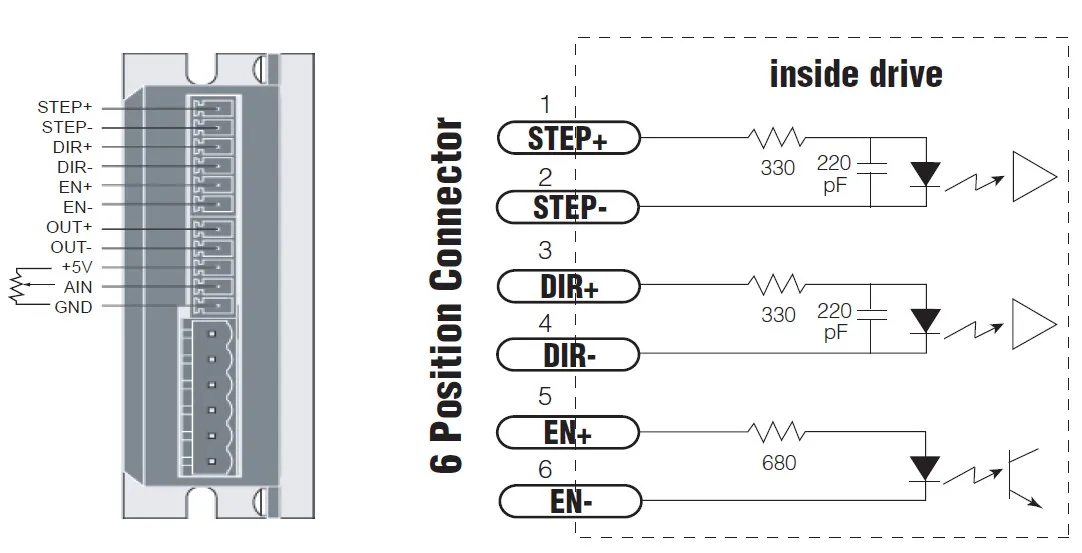
4.2 STEP&DIR Digital Inputs
The S drives are equipped with two high-speed inputs, called STEP and DIR. They accept 5-volt single-ended or differential signals, up to 2 M Hz. EN is a 5 to 12-volt standard digital input that can be used for motor enable, alarm reset, or oscillator speed change. All inputs are configured using the ST Configurator software. The STEP and DIR inputs can be used to connect an indexer, a master encoder, or a CNC hand wheel. They can also be used to connect sensors, switches, and other electronic devices. They can be used as the run/stop and direction inputs for velocity (oscillator) mode.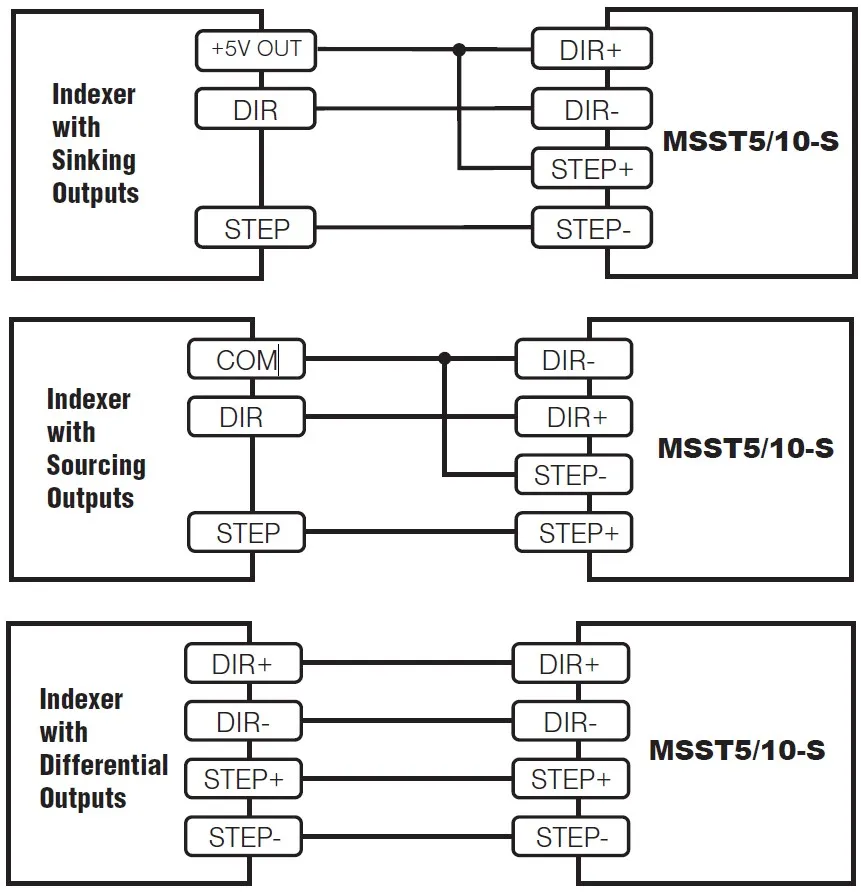
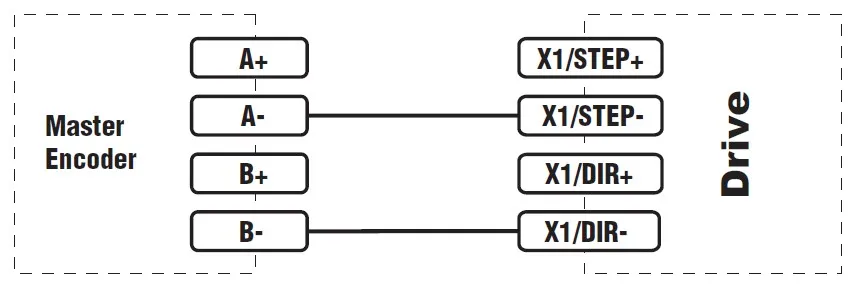
4.3 High Speed Input
PLCs do not commonly use 5-volt logic. Signal levels as high as 24 volts may be connected to the STEP and DIR inputs if external dropping resistors are added as shown below: ▪ For 12-volt logic, add 820 ohm, 1/4 watt resistors ▪ For 24-volt logic, use 2200 ohm, 1/4 watt resistors WARNING: The maximum voltage that can be applied directly to a high speed input terminal is 5 volts. Never apply high voltage AC to an input terminal.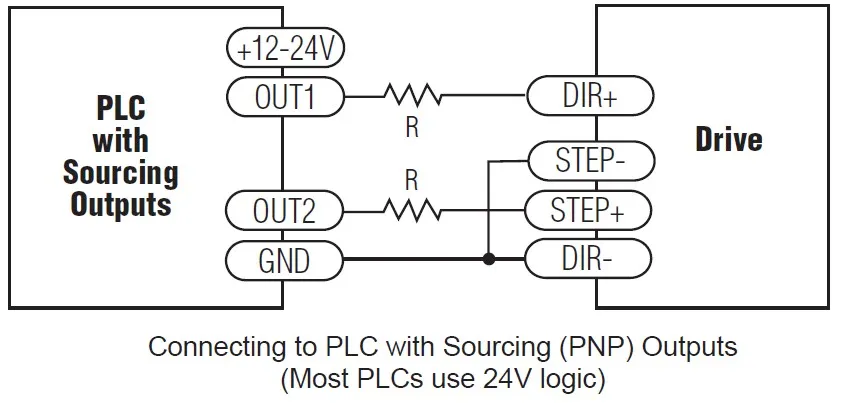
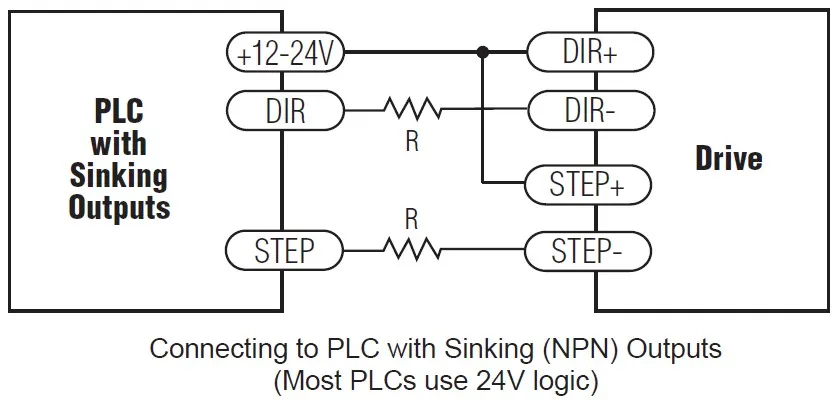
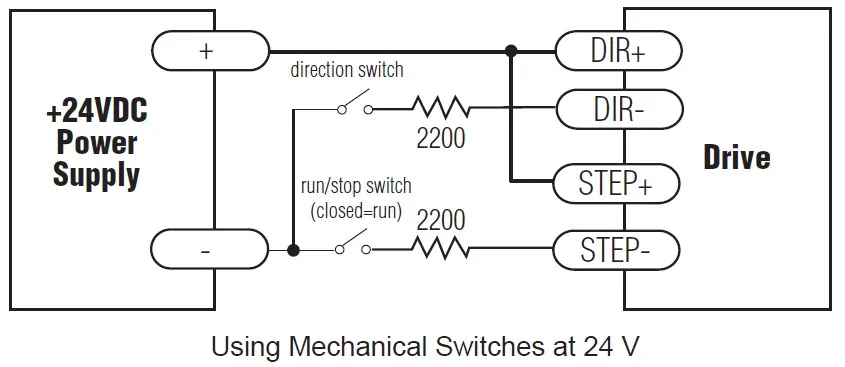
4.4 EN Digital Input
As mentioned above, the STEP and DIR inputs are configured for 5 volt logic. The EN input is designed for operation between 5 and 12 volts. Add 1500ohm to En for 24 volt operation.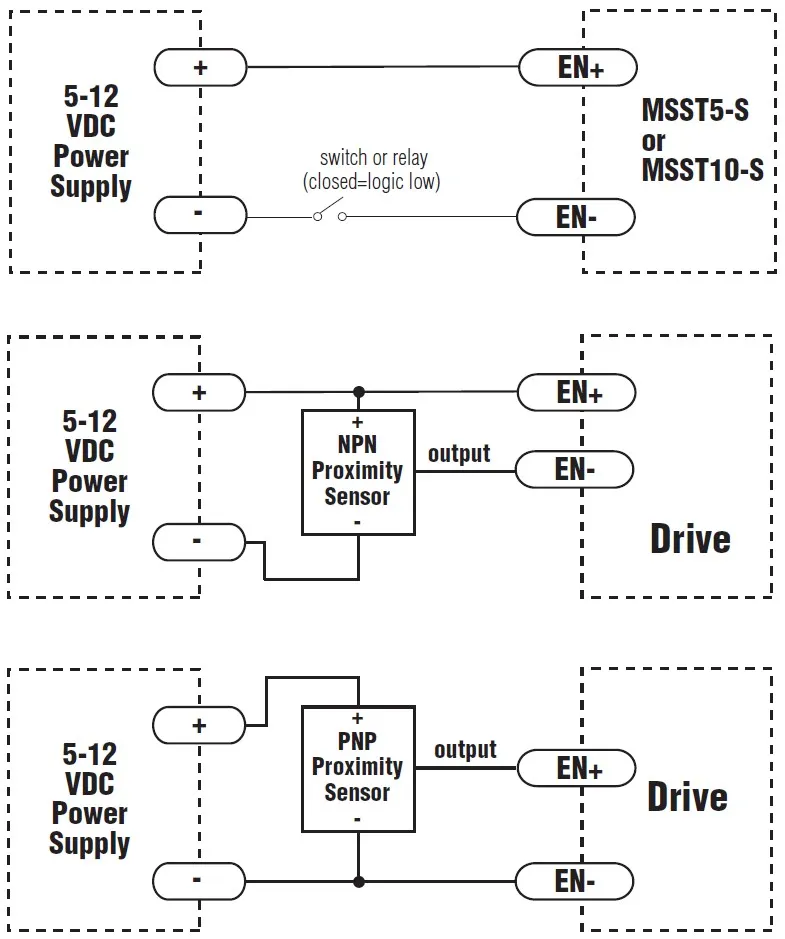
4.5 Analog Inputs
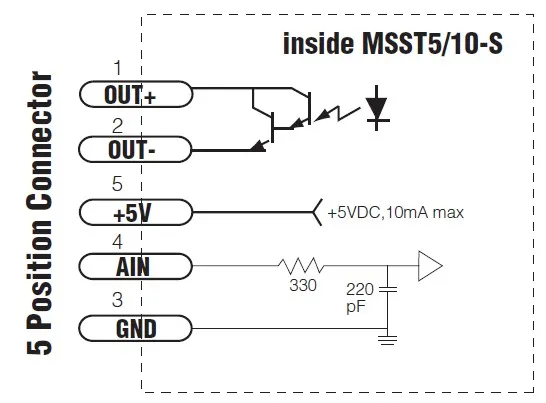
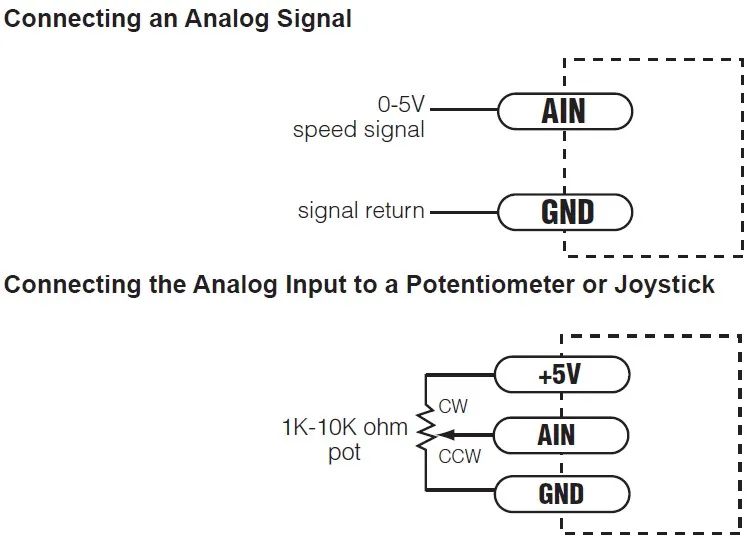
4.6 Connecting the Digital Output
The MSST5-S and MSST10-S drives include one digital output that can be used in one of five ways: Brake: Control an electric brake relay, automatically releasing and engaging as the drive requires Motion: indicates when the motor is moving Fault: closes when a drive fault or alarm condition occurs, the red and green LEDs will flash an error code Tach: produces pulses proportional to the distance traveled (and thereby a frequency that is proportional to motor speed). General purpose: digital output controlled by the SCL SO, FO, IL and IH commands The output has separate + and – terminals and can be used to sink or source current. Diagrams of each type of connection follow. Do not connect the outputs to more than 24VDC. The current through each output terminal must not exceed 10 mA.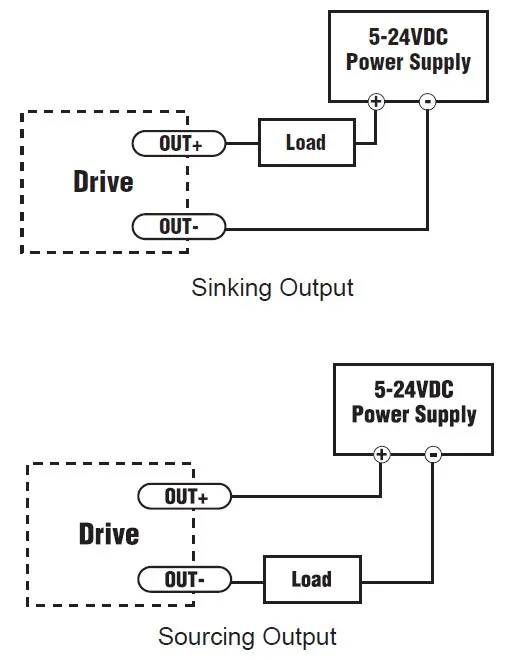