Field Bus Control Option
In present time, fieldbus control system is hot spot in the field of automation control technology, which is being paid more and more attention by users and automatic equipment manufacturers.MOONS' drive and integrated motor products are now available for RS485 Modbus/RTU protocol, CANopen potocal based on CANbus, as well as Ethernet and Ethernet/IP communication protocols. With MOONS' developed SCL serial communication language, and stand-alone Q programmer control mode. It offers great efficiency, reliable, cost effective methods for field bus motion control solutions.
Industry field bus
- CANopen
- • ST Series Two Phase DC Stepper Motor Drives
• STAC Series Two Phase AC Stepper Motor Drives
• Integrated Stepper Motors
• Integrated Step-Servo Motors
• Servo Drives
Command Language

MOONS' Support for Beckhoff and Trio
Currently we provide connection guides for Beckhoff Automation's TwinCAT 2 software and Trio Motion's Motion Perfect software. Users of these software and controller solutions can utilize the EtherCAT Connection Guides to more rapidly and easily incorporate SS-EC drives and motors onto their networks. If you want to integrate StepSERVO drives and motors into your EtherCAT network as fast as possible, these EtherCAT Connection Guides will help you do just that.
EtherCAT Operating Principle
The unique way that EtherCAT works makes it the clear “engineer's choice.” Resource: from WikipediaWhy Use EtherCAT®?
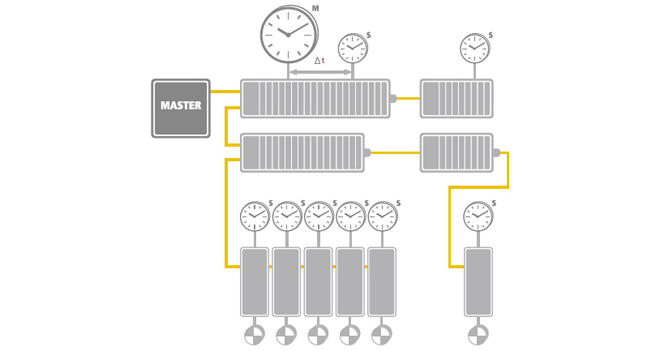
Completely hardware-based synchronization with compensation for propagation delays.
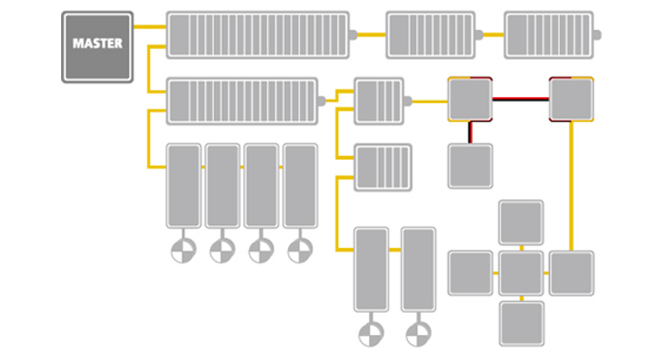
Flexible topology – line, tree or star
EtherCAT utilizes the protocol Safety over EtherCAT allows:
--A single communication system for both control and safety data
--The ability to flexibly modify and expand the safety system architecture
--Pre-certified solutions to simplify safety applications
--Powerful diagnostic capabilities for safety functions
--Seamless integration of the safety design in the machine design
--The ability to use the same development tools for both standard and safety applications
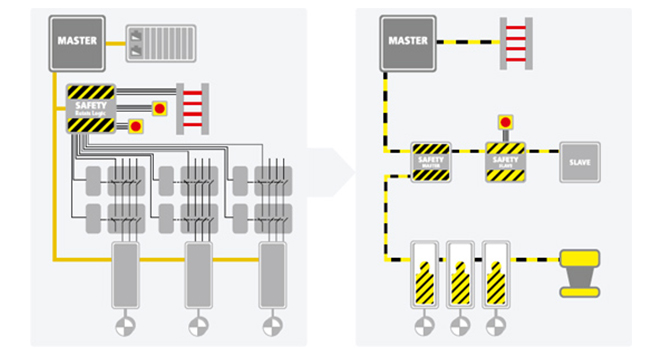
Safety over EtherCAT enables simpler and more flexible architectures than with relay logic
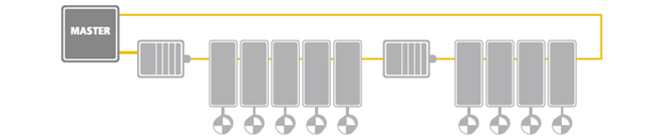
Inexpensive cable redundancy with standard EtherCAT slave devices
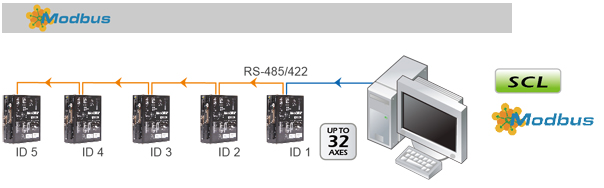
Since Modbus is a master/slave protocol, that means only one node is a master and the others is slave node .Each device intended to communicate using Modbus is given a unique address. In serial networks, only the node assigned as the Master may initiate a command.
A Modbus command contains the Modbus address of the device it is intended for. Only the intended device will act on the command, even though other devices might receive it (an exception is specific broadcast able commands sent to node 0 which are acted on but not acknowledged). All Modbus commands contain checksum information, to allow the recipient to detect transmission errors. The basic Modbus commands can instruct an RTU to change the value in one of its registers, control or read an I/O port, and command the device to send back one or more values contained in its registers.
- Features
- • RS485/422 communication
• Cost effective
• Maximum 32 axes control
• User friendly
Manual:Modbus RTU Manual
Software Download: Modbus/RTU Library Setup 1.0.20.0818
Software Download: Modbus/TCP Library Setup 1.0.18.0929back to top
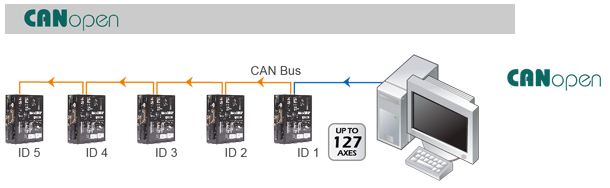
- Features
- • High communication rate
• Communication error tolerance
• Up to 127 axes control
• Standard communication protocol
Manual:CANopen user manual
Software Download:CANopen Test Tool
Motion Control Library:CANopen Libraryback to top
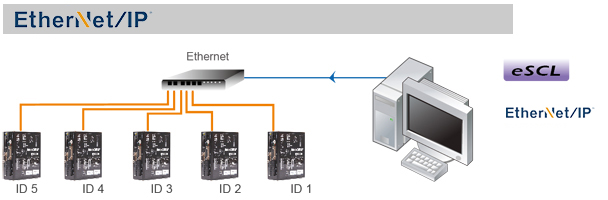
MOONS' has a wide range of products that supports Ethernet/IP protocol, including stepper series, step-servo series, and servo series products. Combine with MOONS' Q programmer control, it offers great range of control options, including various commands, and up to 130 data registers.
- Features
- • Real time motion control
• High Precision
• Easily repeatable
• High speed
• Large number axes control back to top

eSCL is developed based on MOONS' SCL command, it allows the SCL to transfer via Ethernet from the host control to the driver. There are two types of host commands available: buffered and immediate. Buffered commands are loaded into and executed out of the drive's volatile command buffer, also known as the queue. Immediate commands are not buffered: when received by the drive they are executed immediately.
Manual:HOST COMMAND reference
Motion Control Library:SCL Library
Motion Control Library:eSCL Library

- Features
- • Single-Axis motion control
• Stand Alone
• Multi-task
• Conditional Processing
• Math Calculation
• Data register manipulation
• Up to 62 line of command in one segment, and Up to 12 segments in one program.
Manual:HOST COMMAND reference
Software Download:Q programmerback to top