PM Stepper Motors Operating Principles
The structure of Rotary Motors and Linear Actuators is different, as shown in the following figure:
Rotary Motors
Linear Actuators
PM Stepper Motors Schematic Diagrams
Stepper Sequence A two phase step motor with a 7.5-degree step angle is an example of a motor that can be controlled in this way. By reversing the current in one phase, the motor moves one step in a known direction, and by reversing the current in the other phase, it moves one step in the opposite direction. The motor continues to step in the desired direction as the current in each phase is reversed in sequence. These steps are highly accurate, with exactly 48 steps in one revolution for a 7.5-degree step motor. Two types of windings are used in two phase stepping motors: bipolar and unipolar. In a bipolar motor, there is one winding on each phase, and the motor moves in steps as the current in each winding is reversed. This requires a drive with eight electronic switches. In a unipolar motor, there are two windings on each phase, and the phase current is reversed by turning on alternate windings on the same phase. This requires a drive with only four electronic switches. The bipolar operation provides 40% more holding torque than unipolar, as the entire winding is energized in the bipolar arrangement.
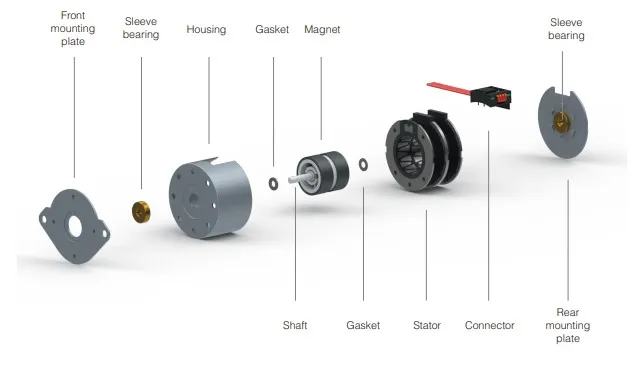
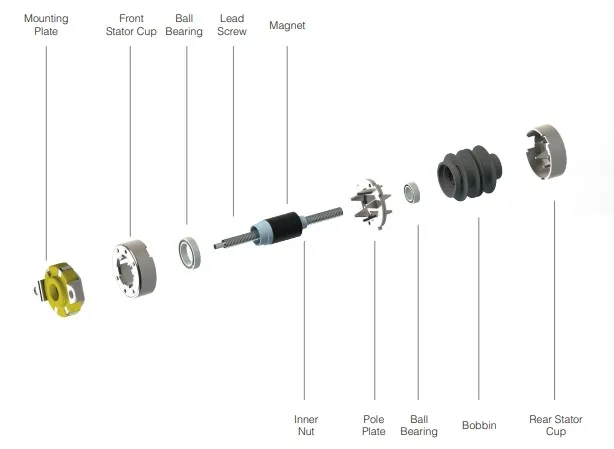
PM Stepper Motors Operating Principles
The operation of a step motor is based on the application of power to the motor windings in response to control signals. This causes the rotor to step forward or backward, or to hold in place.
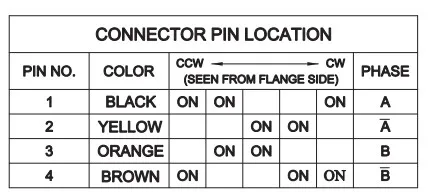