What is PWM control technology?
Pulse Width Modulation is also known as PWM control technology. During the past few years, DC servo motors have undergone significant changes in terms of their structure and control mode. With the development of computers and the continuous emergence of power electronic devices, the use of fully controlled switching power components for Pulse Width Modulation (PWM) control has become more widespread.
Figure 1-12 Schematic diagram of DC PWM control Figure 1-12 illustrates the schematic diagram of a DC motor controlled by PWM using a switch tube. When the gate input signal Up of the switch tube is high, the switch tube turns on, the voltage Ua=Us at both ends of the armature of the DC servo motor increases, and the current at both ends of the armature increases as well. During time t1, the gate input signal becomes low, the switch tube is cut off, the voltage at both ends of the motor armature is 0, and the current Ia at both ends of the motor armature is free-flowing through the diode VD2. As a result of time t2, the gate input becomes high again, and the action of the switch tube repeats itself. As a result, within a time period T=t1+t2, the average voltage at both ends of the DC servo motor armature is: Ua= (t1Us+0) / (t1+t2) = t1Us / T= αUs Where: α=t1/T is the duty cycle, which represents the ratio of the turn-on time of the power switch tube to the cycle in a cycle T, and its value ranges from 0≤α≤1. Therefore, when the power supply voltage Us remains unchanged, the average voltage Ua at both ends of the armature depends on the size of the duty cycle α. Changing the value of α, the average value of Ua can be changed, to achieve the purpose of speed regulation, which is the control principle of DC PWM speed regulation. The duty cycle is an important parameter in PWM speed regulation. There are three ways to change the duty cycle: 1) Fixed width frequency modulation method: keep t1 unchanged, only change the value of t2, so that the period T or chopper frequency changes; 2) Width modulation frequency modulation method: keep t2 unchanged, only change the value of t1, so that the period T or chopper frequency changes; 3) Fixed frequency width adjustment method: simultaneously change t1, t2, and keep the period T or chopper frequency unchanged. As the chopper frequency is changed in the first two methods, it is possible to cause oscillations if the chopper frequency is close to the natural frequency of the system. As a result, these two methods are seldom used, and the fixed frequency and width modulation method of speed regulation is generally used. Reversible PWM speed control systems can drive DC servo motors in both positive and reverse modes, which can be categorized into unipolar and multipolar drives. 1) Unipolar reversible driving mode Unipolar drive means that in a PWM control cycle, the voltage polarity of the motor changes singularly. There are two kinds of unipolar driver circuits. One type of circuit is called a T-shaped circuit, which requires positive and negative power supplies, which is equivalent to two irreversible combinations. As its circuit shape is similar to the letter "T", it is referred to as a T-shaped circuit. Since the current of the T-shaped unipolar drive cannot be reversed, and the working condition of the forward and reverse switching of the two switch tubes is that the armature current is zero, the motor dynamic performance is poor. A driver circuit of this type has been rarely used. Another type of unipolar driver circuit is called an H-shape, that is, a bridge circuit. The motor dynamic performance in this circuit is good, so it is widely used in various control systems.
Figure 1-13 Schematic diagram of H-shaped unipolar reversible PWM drive system As shown in the figure above, the system consists of four switching tubes and four freewheeling diodes, which are powered by a single power supply. In the figure, Up1 to Up4 represent the trigger pulses for switch tubes VT1 to VT4. As the motor turns forward, the synchronous trigger signal is added to VT1 and VT2 and the state is reversed. At the same time, Up3 is low and Up4 is high, so that the voltage at both ends of the armature is UAB≥0; When the motor is reversed, the synchronous trigger signal is added to VT3 and VT4 and the state is opposite. At the same time, Up1 is low and Up2 is high, so that the voltage at both ends of the armature is UAB≤0. When the motor is in forward rotation, VT1 drive signal, armature voltage and current waveforms are shown in Figure 1-14.
Figure 1-14 VT1 drive signal, electric drive voltage and current waveforms When the motor is required to accelerate operation under a large load, the armature average voltage is greater than the back EMF, that is, Ua>Ea. When 0≤t<t1 in each PWM control cycle, VT1 is on, VT2 is off, and the current Ia direction flows along loop 1, from A to B through VT1 and VT4 through the armature winding. When t1≤t<T, VT1 is cut off and the power supply is disconnected. Under the action of the back EMF, the current Ia direction flows along loop 2, freewheeling through VT4 and VD2, and the armature current direction is from A to B. Moreover, due to the clamping effect of the diode, although Up2 is high, VT2 does not actually conduct and the average current Ia>0. When the motor is operating without load or light load, the average voltage is almost comparable to the EMF, that is, Ua≈Ea. In each PWM control cycle, when 0≤t<t1, VT2 cut-off, the current Ia direction first flows along loop 4, first through VD4, VD1 to the power supply, the direction from B to A, the motor works in the regenerative braking state; When the current decreases to 0, VT1 is on, and the current Ia direction flows along loop 1, from A to B and through VT1, VT4, and the motor is in the electric state. When t1≤t<T, VT1 cut off, the current Ia direction first flows along loop 2, through VT4, VD2, the direction is from A to B, the motor works in the freewheeling state; When the current decreases to 0, under the action of the back EMF, the current Ia direction flows again along loop 3, from B to A through VD4, VT2, and the motor works in the state of energy consumption braking. According to the above analysis, in each PWM control cycle, the motor runs in four states of regenerative braking, electric, freewheeling electric and energy consumption braking in turn, and the current fluctuates up and down around the horizontal axis. When the motor is running with deceleration, the armature average voltage is less than the back EMF, that is, Ua< Ea. When 0≤t<t1 in each PWM control cycle, under the action of the back EMF, the current Ia direction flows along loop 4 and flows to the power supply through VD1~VD4, from B to A, and the motor is in the regenerative braking state. When t1≤t<T, VT2 is on and VT1 is off. Under the action of the back EMF, the current Ia direction flows along loop 3, from B to A through VD4 and VT2, and the motor works in the state of energy consumption braking. Unipolar reversible PWM drive is characterized by only two driving pulses, simple circuit, small current fluctuation, can achieve four-quadrant operation, is a widely used driving mode. 2) Bipolar reversible driving mode In a bipolar drive, the voltage at both ends of the armature alternates between positive and negative during a PWM cycle. Like unipolar, bipolar driver circuits are divided into T-shaped and H-shaped. Since the switch tube has to bear higher reverse voltage in the T-shaped equivalent circuit, its application is limited in the servo motor system with large power. The H-shaped drive circuit does not have this problem and is widely used. The main circuit of H-shaped bipolar reversible PWM drive system is the same as Figure 1-13. The four switch tubes VT1 to VT4 are divided into two groups, VT1 and VT4 are one group, and VT3 and VT2 are the other group. The switch tubes of the same group are synchronously on or off, while the switch tubes of different groups are in the opposite state of the switch tubes of the other group. In each PWM control cycle, when the control signals Up1 and Up4 are high, Up2 and Up3 are low, VT1 and VT4 are on, VT2 and VT3 are off, and the voltage UAB=Us; When the control signals Up2 and Up3 are high, Up1 and Up4 are low, VT2 and VT3 are on, VT1 and VT4 are off, and the voltage UAB=-Us. Therefore, the two ends of the armature are alternating positive and negative, which is called "bipolar". In a PWM control cycle, the armature voltage undergoes positive and negative changes twice, and the average armature voltage is: Ua=(t1/T) * Us - (T-T1)/ T * Us =(2α-1) * Us According to the above formula, the average armature voltage depends on the magnitude of the duty cycle α for the drive of bipolar PWM control. When α=0, Ua=-Us, the motor reverses, and the speed is the highest. When α=½, Ua=0, the motor stops, but there is still an alternating current flowing through the motor, so that the motor generates high-frequency oscillation, which is beneficial to overcome the static friction of the motor load and improve the dynamic characteristics of the motor. When α=1, Ua=Us, the motor is turning forward and the speed is the highest.
Figure 1-15 Bipolar drive signal Up1 and current waveform Figs. 1-15 show the drive signal Up1 and the current waveform in the three cases of motor forward rotation, reverse rotation and no rotation. When the motor is required to move forward under a large load, the average armature voltage is greater than the back EMF, that is, Ua>Ea. In each PWM control cycle, when 0≤t<t1, VT1, VT4 conduction, VT2, VT3 cut-off, current Ia direction from A to B; When t1≤t<T, VT2 and VT3 are on, and VT1 and VT4 are cut off. Although reverse voltage is applied to both ends of the winding, the current direction will not change due to the large load current of the winding, but the decrease of current amplitude is larger than that of unipolar driving, so the current fluctuation is large. The current waveform is shown in Figure 1-15(a). When the motor is required to run in reverse at a large load, the situation is just the opposite, and the current waveform is shown in Figure 1-15(b). When the motor is required not to turn, α=1/2 and the average armature voltage Ua=0. In each PWM cycle, when 0≤t<t1, VT1, VT4 conduction, VT2, VT3 cut-off, current Ia direction from A to B; When t1≤t<T, VT2 and VT3 are on, VT1 and VT4 are off, and the direction of current Ia is from B to A, so the current fluctuates around the horizontal axis with an average value of 0. The current waveform is shown in Figure 1-15(c). Bipolar drives allow the motor to run at low speeds and have good low-speed stability. However, when operating, because the four switch tubes are in the switching state, the power loss is significant, so the bipolar drive is only suitable for small and medium-sized DC servo motors. To prevent the same bridge from passing under the switch tube, "dead zone" protection is added.
Principle of PWM control
DC servo motors can be controlled by two different methods: excitation control, which contains the magnetic flux, and armature voltage control, which controls the armature voltage. As most DC servo motors use armature voltage control modes for speed regulation, this paper discusses the method of controlling armature voltage with PWM control technology to realize speed regulation in DC servo motors.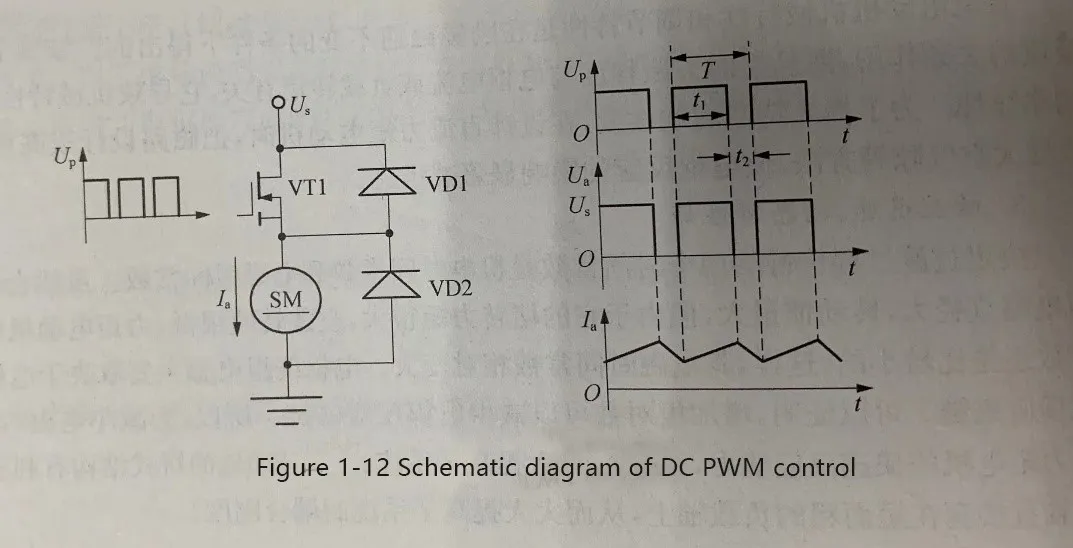
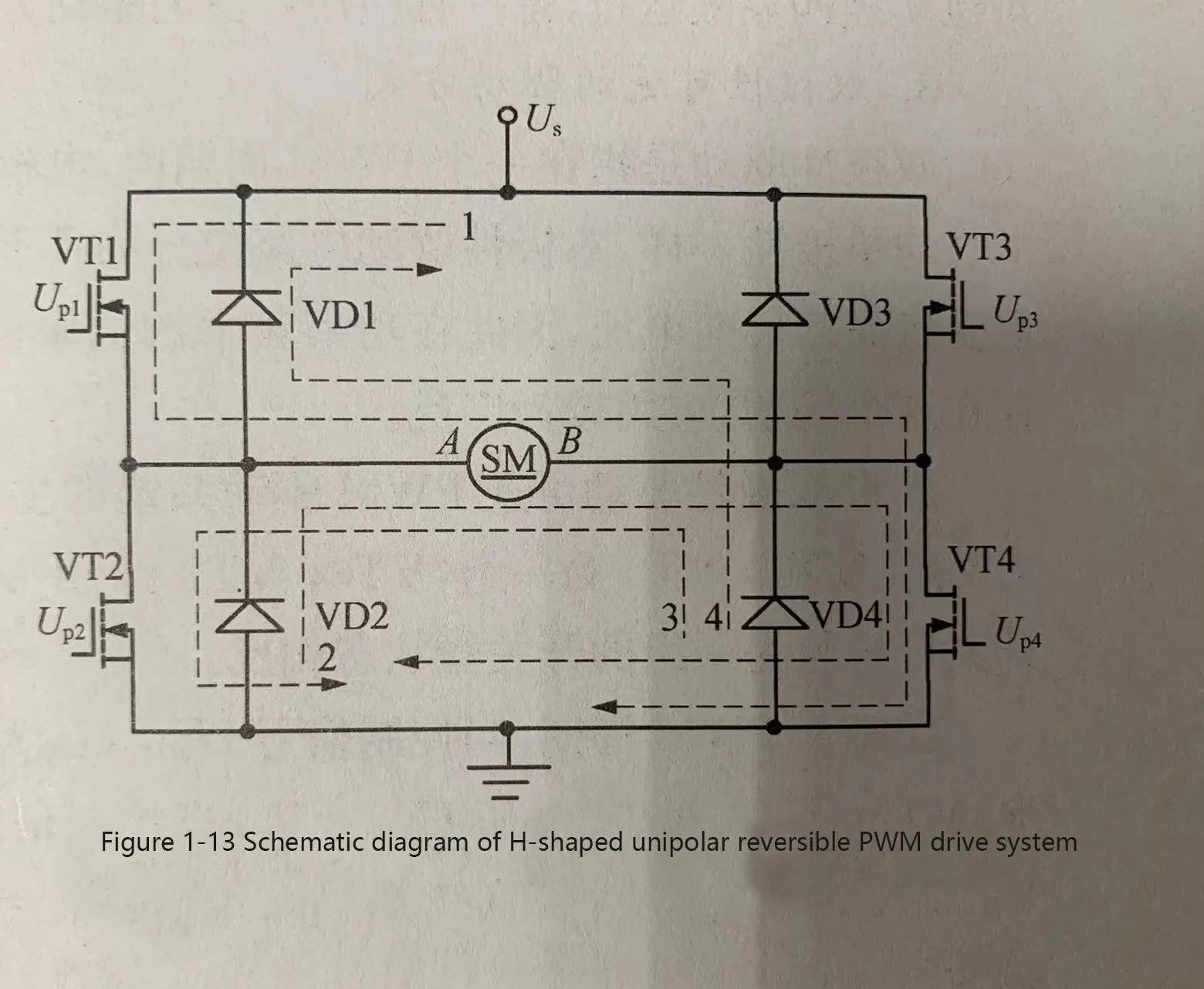
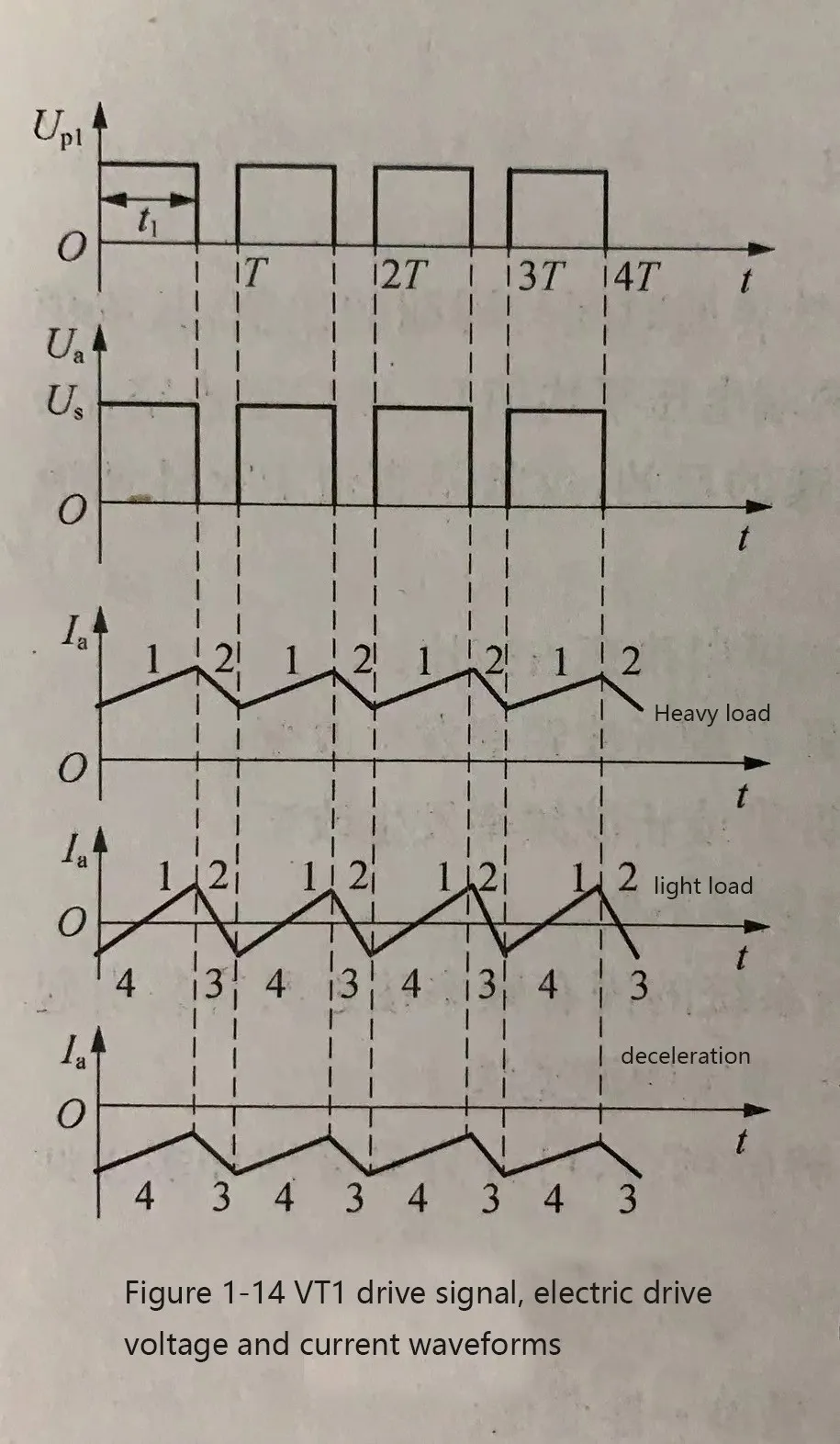
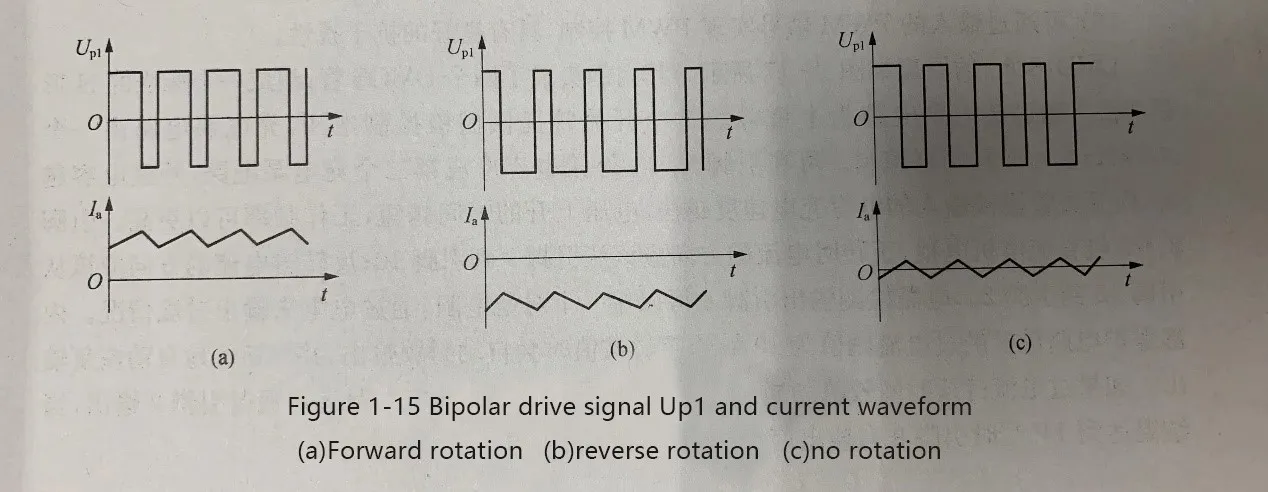