Step Motor – Basic Structure & Operation
• Basic Structure
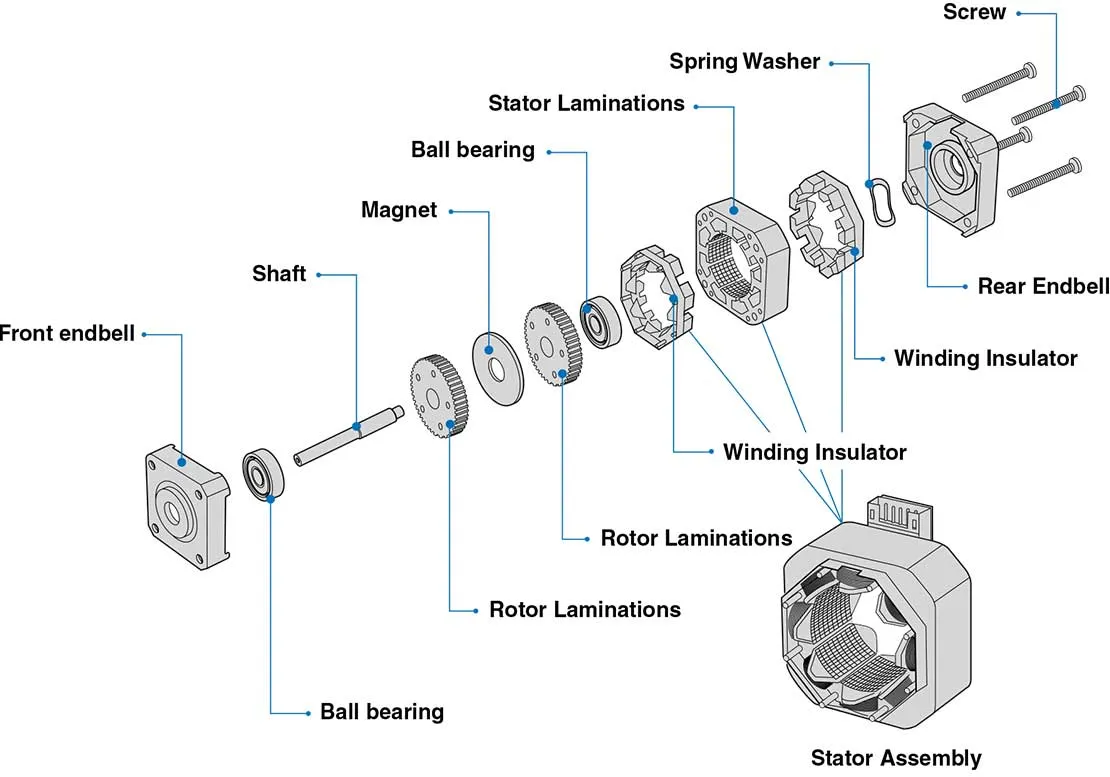
• Operating Principles
In response to each individual control pulse and direction signal, the drive applies power to the motor windings to move the rotor forward, backward, or hold it in place. If both phases of a 1.8-degree two-phase step motor are energized with DC current, the motor will stop rotating and hold in place. With a rated DC current, the motor can hold maximum torque in place, is the rated holding torque. The motor will move one step (1.8 degrees) in a known direction if the current in one phase is reversed. If When the current in the other phase was reversed, the motor would move 1 step (1.8 degrees) in the opposite direction. The motor continues to step in the desired direction as the current is reversed in each phase. The steps are very accurate. In one revolution of a 1.8-degree step motor, there are exactly 200 steps. In two-phase stepping motors, there are two types of windings: bipolar and unipolar. Each phase of a bipolar motor has one winding. As the current in each winding is reversed, the motor moves in steps. This requires a drive with eight electronic switches. Each phase of a unipolar motor has two windings. Each phase has two windings connected in opposite directions. By turning on alternate windings on the same phase, phase current can be reversed. This requires a drive with only four electronic switches. The bipolar operation typically provides 40% more holding torque than unipolar because 100% of the windings are energized.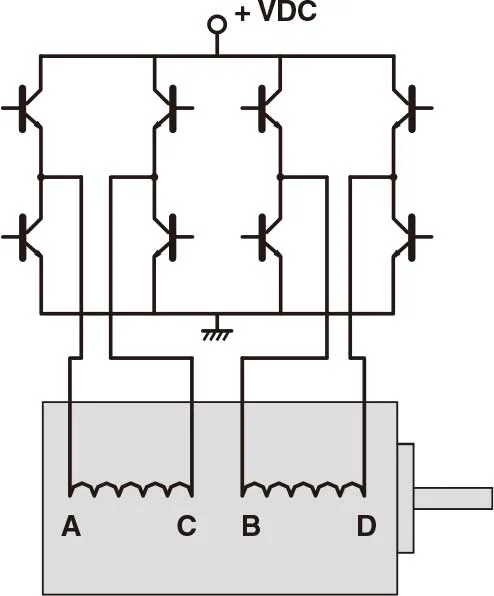
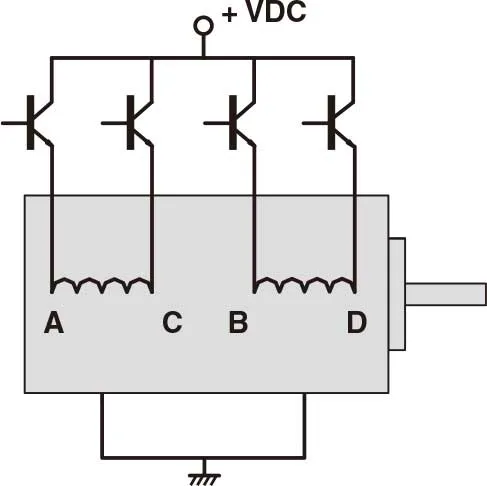
• Precise Positioning Control
A stepper motor rotates with a fixed step angle, just like the second hand of a clock. This angle is called "basic step angle." MOONS' offers several types of "basic step angle" as standard motors: 2-phase stepping motors with a basic step angle of 0.9° and 1.8° and 3-phase stepping motors with a basic step angle of 1.2°. Aside from the standard motor, MOONS' also offers stepper motors with other "basic step angle." These are 0.72°, 1.5°, 3.6°, and 3.75°. These motors are not listed in this catalog, please contact MOONS' for more information.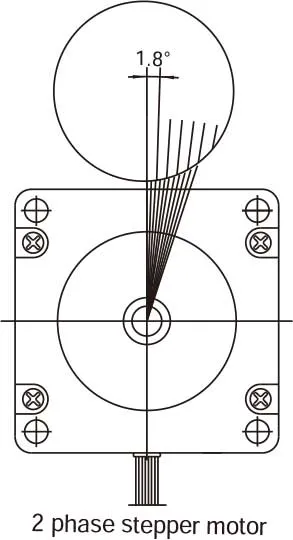
• Easy Control with Pulse Signals
Below is a system configuration for high-accuracy positioning. Using pulse signals from the controller, the stepping motor's rotation angle and speed can be accurately controlled.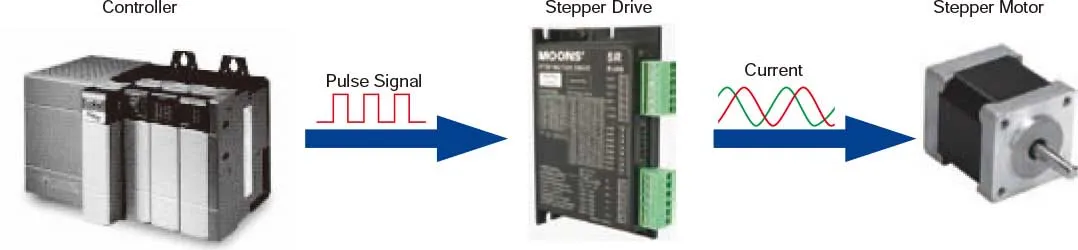
• What is a Pulse Signal?
An electrical pulse signal is a signal whose voltage level alternates between ON and OFF repeatedly. One pulse is counted for each ON/OFF cycle. With one pulse, the motor output shaft turns one step. Signal levels corresponding to voltage ON and OFF conditions are designated as "H" and "L."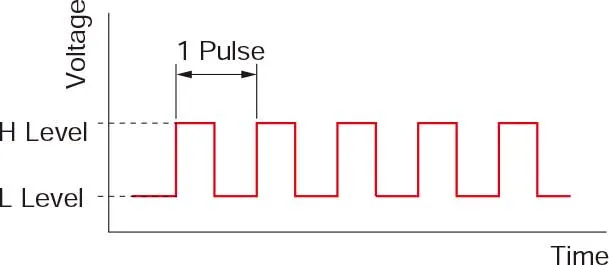
• The length of Rotation is Proportional to the Number of Pulses
The length of rotation of a stepping motor is proportional to the number of pulse signals (pulse number) given to the driver. A stepper motor's rotation (rotation angle of the motor output shaft) is related to pulse number as follows:
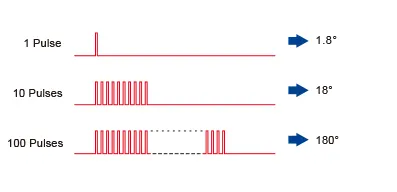
• The Speed is Proportional to the Pulse Frequency
Stepper motor speed is proportional to the frequency of pulse signals given to the driver. Following is the relationship between pulse frequency [Hz] and motor speed [r/min]:
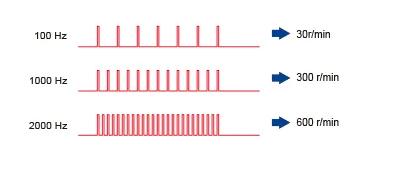
• Generating High Torque with a Compact Size
In addition to generating high torque, stepper motors are compact in size. Their excellent acceleration and response make them ideal for torque-demanding applications where the motor must be started and stopped frequently. MOONS' also offers geared motors if greater torque is required at low speeds.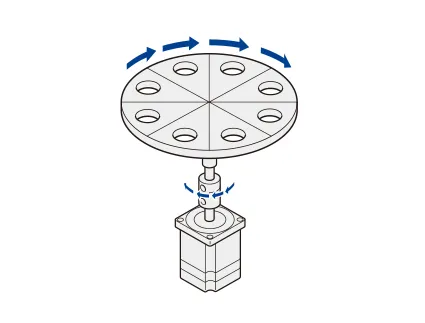
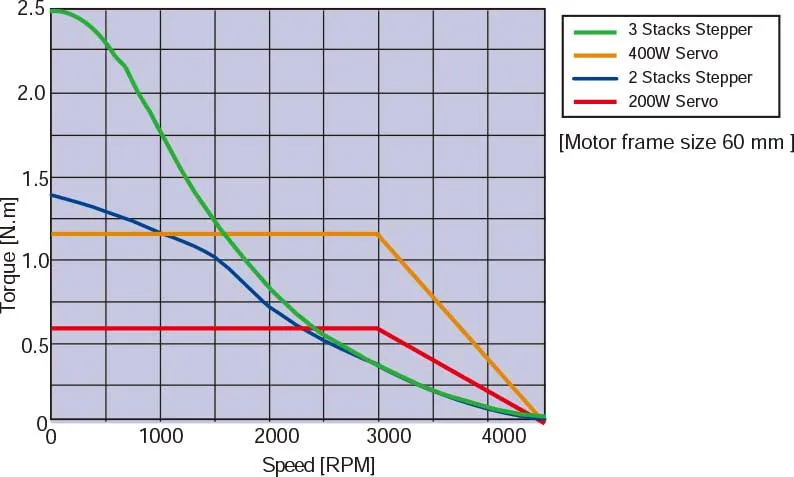
• The Motor Holds Itself at a Stopped Position
When the windings are energized, the stepper motor has full torque at standstill. The motor can be held at a stopped position without using a mechanical brake.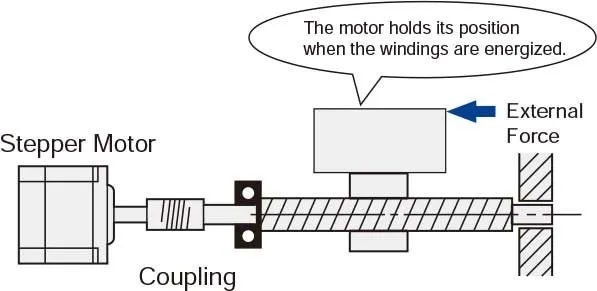
• Motor with Electromagnetic Brake
In vertical operations or when an external force is applied, the motor no longer holds the stopped position once the power is cut off, resulting in it losing its self-holding torque. Lifts and similar applications require electromagnetic brake motors.
• Closed Loop Servo Control Stepper Motors
In the world of stepping motors, the
is a technological revolution that combines stepping motors with servo technology to create an exceptional product. Using the
, the performance is greatly improved to be much more Intelligent, Efficient, Compact, Accurate, Fast, and Smooth.
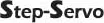
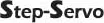
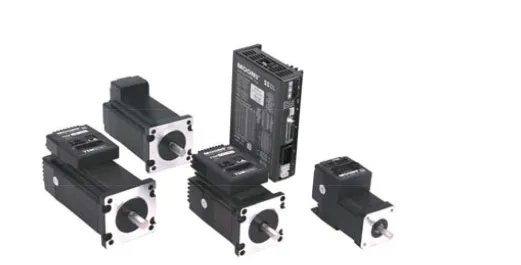
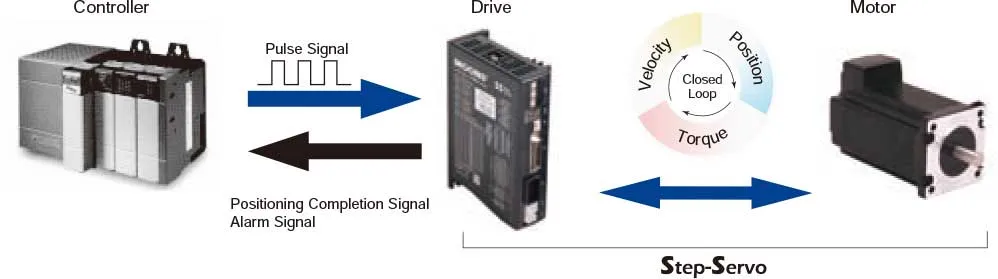