How to Reduce the Noise & Resonances of Stepper Motors
The advantages of stepper motors are their simple structure, ease of control, safety, low cost, high torque, etc. Several types of open-loop control systems use stepper motors as high-performance digitized electrical components. The stepper motor, however, has a disadvantage in that it is noisy at low speeds. Resonances and noise are primarily caused by the drive circuit and its mechanical structure. Higher harmonics are the main cause of driving circuit noise. Stepper motors are driven by square wave currents, which must contain many harmonics, causing vibration and noise. A cost-effective, high-performance step drive is available in the SR series. High torque, low noise, and low vibration are all features of the design based on advanced digital current control technology. Other parameters, such as the running current and microstrip resolution, can be selected via a switch.
MOONS' Drive Circuit Resonance Solution
Microstep Emulation Low-resolution systems can still provide smooth motion with Microstep Emulation. Using low-resolution step pulses, the drive can create fine-resolution motions. Enhances overall system performance
Torque Ripple Smoothing Step motors have an inherent torque ripple at low speeds that can affect the motor's motion profile. This torque ripple can be countered by applying a negative harmonic. At low speeds, the motor moves much more smoothly. Produces smoother motion at low speeds
Also introduced by MOONS' are the ST series step actuators with communications and the STF series step actuators, which are suitable for industrial control applications. During motor movement, the rotating part or rotor oscillates around a new position before stopping, and this oscillation time is called the settling time. By adjusting the drive parameters without changing the overall design, vibration may not be reduced. The best solution here is to use a damper. In step motor systems, dampers reduce resonances, reduce noise, and improve response time. They are mounted between the motor and machine, and work by reducing shock impulses and dissipating the kinetic energy in resonances.
MOONS' Mechanical Resonance Solution
Fast Response When performing fast point-to-point moves, a damper can enhance the system's transient response and decrease settling time. Control accuracy is improved as a result. 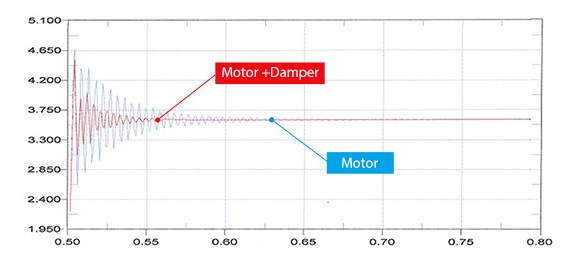
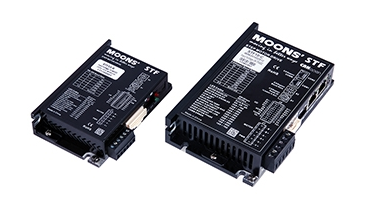
Features
Anti-Resonance There is a natural tendency for step motor systems to resonate at certain speeds. Automatic damping is applied to the control algorithm by SR drives based on the system's natural frequency. This greatly improves midrange stability, allows higher speeds and greater torque utilization, and also improves settling times. Improves motor performance and speeds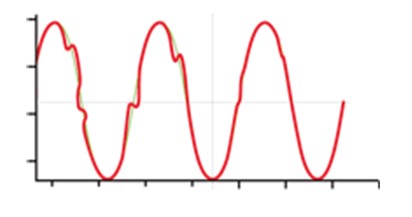
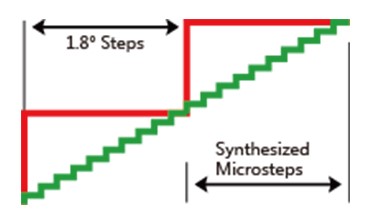
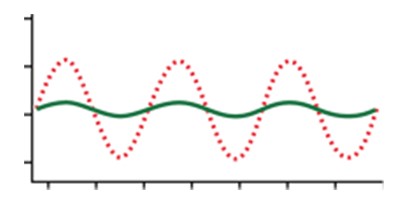
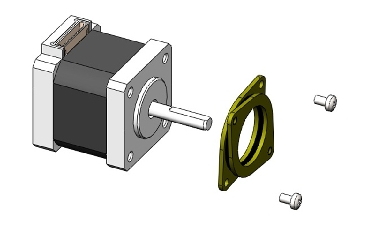
Features
Anti-Resonance, less noise, and Torque Ripple Smoothing Stepper motors have an inherent low-speed torque ripple that can affect their motion. At certain speeds, torque ripples can cause resonances to build up in some systems. As a result, the motor may stall or make noise. MOONS' dampers use energy-absorbing rubber to reduce resonances and vibrations. At low speeds, this can greatly improve system stability, eliminate noise, allow much smoother motion, and provide greater torque utilization at higher speeds.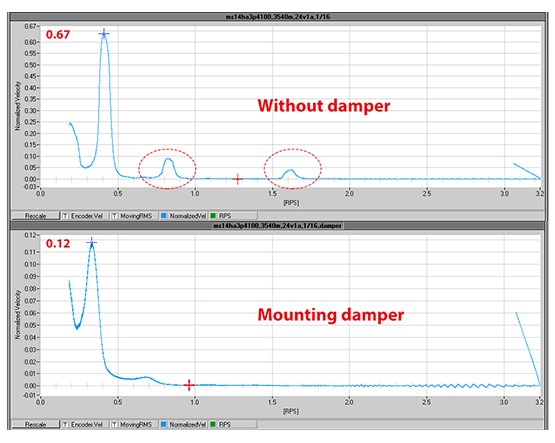
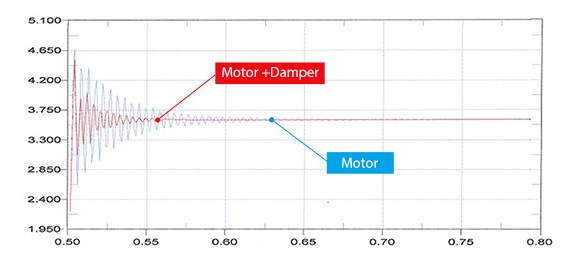