NEW NEMA17 Series Flat Type Stepper Gearmotors
MOONS' is pleased to announce the release of the new NEMA17 series flat type stepper gearmotors. These new stepper gearmotors are equipped with flat type gearhead with a ratio of 5, 10, 25. With the same frame size and output torque, the axial length of the motor is greatly shortened, saving more space for your design. 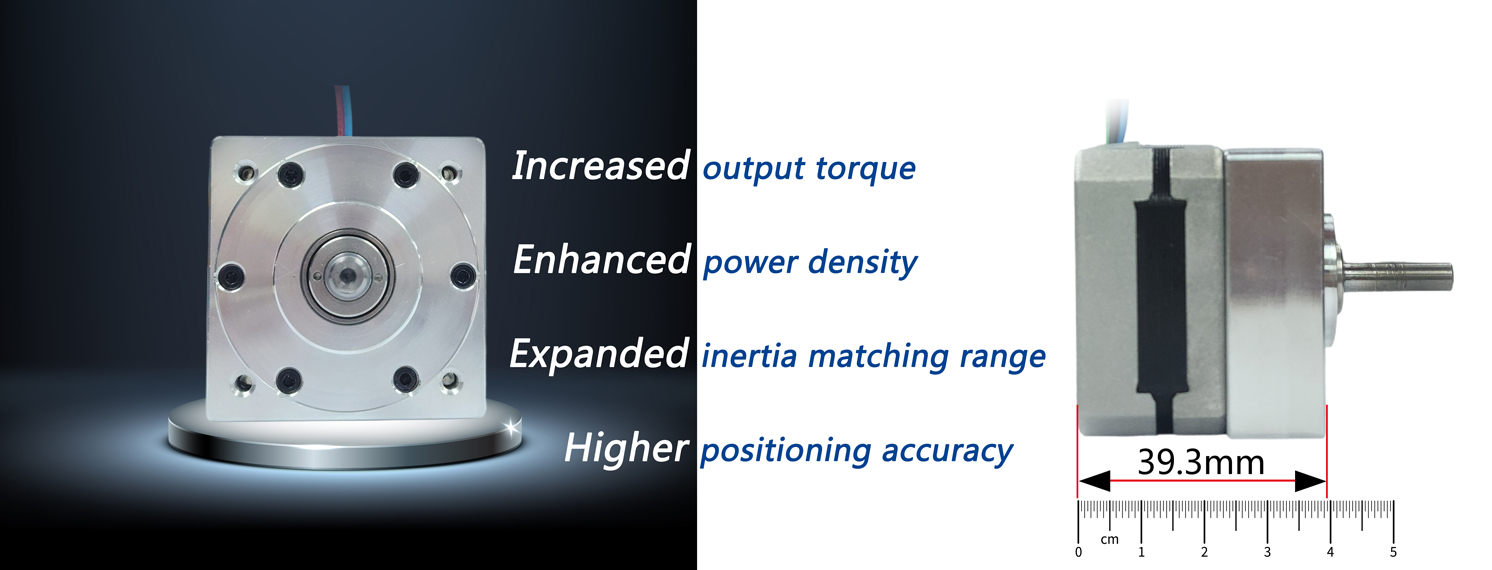
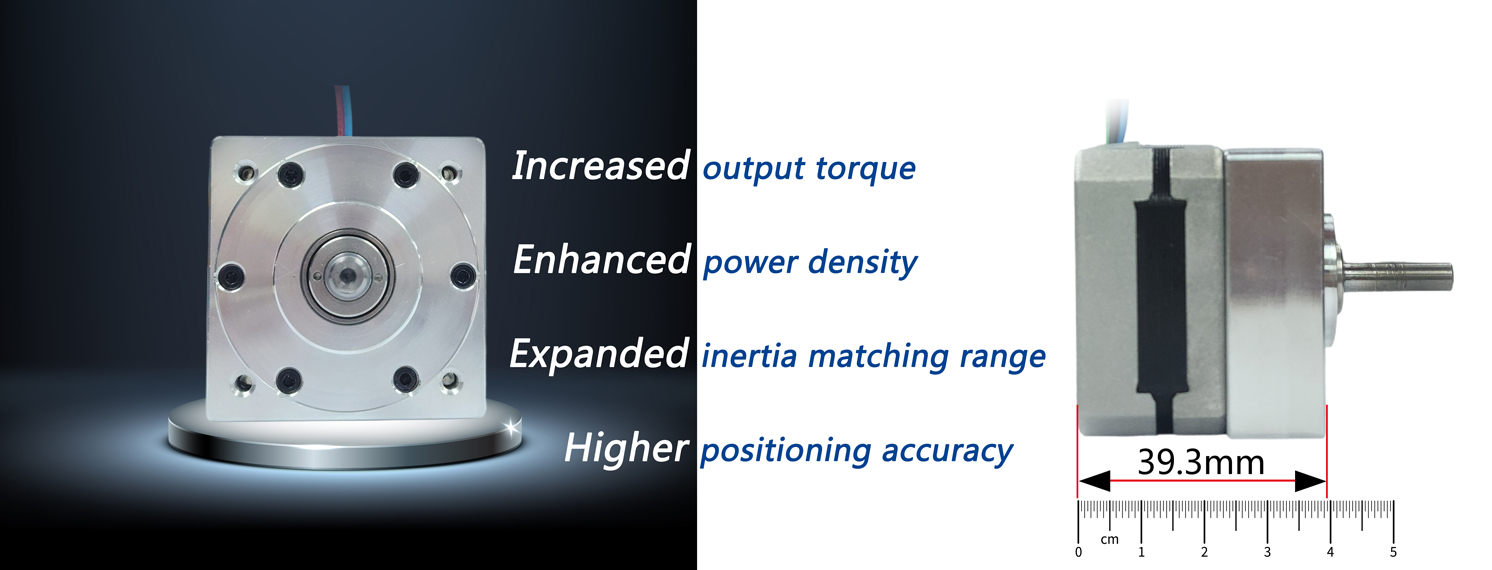
1. Overview of stepper motor with gearboxes
Stepper gearmotor, an efficient and compact unit composed of a motor and a gearbox, significantly enhances the output torque and power density of the motor assembly. Compared to conventional motors, gearmotors substantially save on design space and increase design flexibility under similar working conditions.
From an application standpoint, the ability to interchange gearboxes of various specifications modularly allows the motor components to meet diverse operational demands, thereby greatly expanding the motor's range of applications.
From an application standpoint, the ability to interchange gearboxes of various specifications modularly allows the motor components to meet diverse operational demands, thereby greatly expanding the motor's range of applications.
2. Motor inertia matching
Rotational inertia is the measure of a rigid body's resistance to changes in rotational motion around an axis, essentially representing an object's inertia towards rotational movements. It significantly impacts the precision, stability, and dynamic response of a motor system. In practical applications, the ratio of load inertia (translated to the motor shaft) to the motor's inertia must be kept within reasonable limits. An excessively high ratio can lead to system oscillations or even loss of control.
The motor's high positioning accuracy and stability necessitate rapid stabilization at the target position, meaning the system's adjustment time should be minimized. This adjustment time includes the rise time and the time taken for any overshoot to stabilize within the steady-state error. Given fixed control and adjustment parameters, these factors are directly linked to the rate of change in the motor's tracking control commands, i.e., associated with the system's power change rate. The power change rate of the load is:
In the formula, P, T, ω, and J denote power, torque, rotational speed, and moment of inertia, respectively. The subscripts M and L refer to the motor and the load, respectively. Calculate the first derivative of the load power change rate with respect to the load moment of inertia JL:
It is evident that the load's power change rate is maximized when the load moment of inertia equals the motor's moment of inertia, a condition known as inertia matching. In practical terms, given considerations of motor versatility and cost, a load-to-motor inertia ratio of less than 3:1 is considered ideal. For a gearmotor with a ratio of i, the load inertia equivalent on the motor's output side is:
Meeting the ideal inertia ratio allows the geared motor to accommodate a load inertia range that is i2 times larger than that of a standard motor, significantly broadening the motor's application range. Moreover, under the same load inertia conditions, the geared motor achieves a lower inertia ratio and superior control performance.
The motor's high positioning accuracy and stability necessitate rapid stabilization at the target position, meaning the system's adjustment time should be minimized. This adjustment time includes the rise time and the time taken for any overshoot to stabilize within the steady-state error. Given fixed control and adjustment parameters, these factors are directly linked to the rate of change in the motor's tracking control commands, i.e., associated with the system's power change rate. The power change rate of the load is:



3. Features of MOONS' NEMA 17 series stepper gearmotors
Through the reasonable matching of motor and gearbox, MOONS' NEMA 17 series stepper gearmotor has the following characteristics compared to traditional stepper motors with the same frame size and same motor length:
• Enhanced power density
Consider the MS17HD5 series paired with a 5-ratio gearhead as an example. This motor has dimensions of 39.3mm in length and weighs 0.24g. In contrast, the same-sized MS17HD2 series measures 39.8mm in length and weighs 0.28g. Despite the nearly identical weights, the torque density (static torque/motor weight) of the MS17HD5 with gearhead is 4.167Nm/kg, 2.33 times higher than that of the MS17HD2 series, representing a significant improvement in motor torque density.
• Expanded inertia matching range
Regarding inertia matching, the range of load inertia the motor can accommodate has expanded from 57-171 gcm2 to 426-1426 gcm2, significantly broadening the motor's application range.
• Higher positioning accuracy
In terms of positioning accuracy, taking the MS17HD5 series as an example, equipped with a 5-ratio gearhead, the motor length is 39.3mm, and the overall output step angle is 0.36 degrees. In comparison, the MS17HD2 series with the same volume has a length of 39.8mm and a step angle of 1.8 degrees., the motor positioning accuracy is increased by 5 times, and the smoothness and vibration suppression of the motor are also improved.
• Enhanced power density
Consider the MS17HD5 series paired with a 5-ratio gearhead as an example. This motor has dimensions of 39.3mm in length and weighs 0.24g. In contrast, the same-sized MS17HD2 series measures 39.8mm in length and weighs 0.28g. Despite the nearly identical weights, the torque density (static torque/motor weight) of the MS17HD5 with gearhead is 4.167Nm/kg, 2.33 times higher than that of the MS17HD2 series, representing a significant improvement in motor torque density.
• Expanded inertia matching range
Regarding inertia matching, the range of load inertia the motor can accommodate has expanded from 57-171 gcm2 to 426-1426 gcm2, significantly broadening the motor's application range.
• Higher positioning accuracy
In terms of positioning accuracy, taking the MS17HD5 series as an example, equipped with a 5-ratio gearhead, the motor length is 39.3mm, and the overall output step angle is 0.36 degrees. In comparison, the MS17HD2 series with the same volume has a length of 39.8mm and a step angle of 1.8 degrees., the motor positioning accuracy is increased by 5 times, and the smoothness and vibration suppression of the motor are also improved.
Model | MS17HD2 | MS17HD5+gearbox |
---|---|---|
Step Angle(°) | 1.8 | 0.036-0.72 |
Frame Size(mm) | □42.3 | □42.3 |
Length(mm) | 39.8 | 39.3 |
Rated Current(A) | 1.5 | 1.5 |
Holding Torque(Nm) | 0.5 | 1.0 |
Weight(kg) | 0.28 | 0.24 |
Holding Torque/Weight(Nm/kg) | 1.785 | 4.167 |
Rotor Inertia(gcm2) | 57 | 20 |
Gearbox Inertia(gcm2) | - | 73.88 |
Load Inertia Range(gcm2) | 57-171 | 426-1426 |
• Increased output torque
In terms of torque, when coupled with a gearbox, the motor achieves higher torque at lower speeds. By comparing the torque-frequency curves of the MS17HD2 and the MS17HD5+ with a gearbox, it's evident that as the speed decreases, the gearmotor gains a more significant increase in torque relative to conventional motors. Across the entire frequency range, the gearmotor achieves complete coverage of the torque-frequency curve.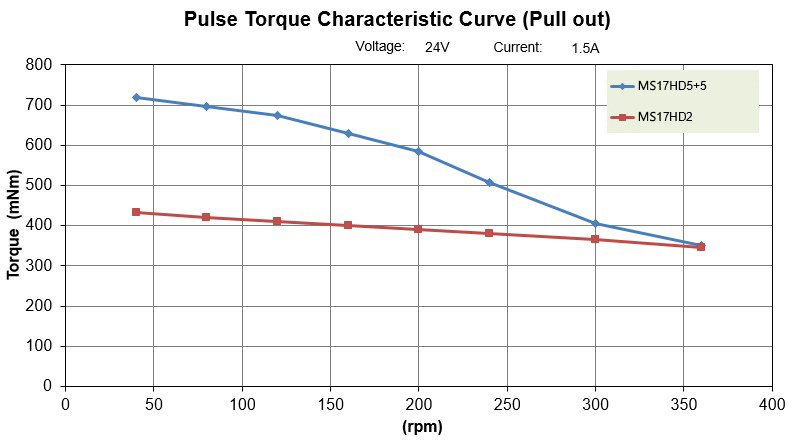
In terms of torque, when coupled with a gearbox, the motor achieves higher torque at lower speeds. By comparing the torque-frequency curves of the MS17HD2 and the MS17HD5+ with a gearbox, it's evident that as the speed decreases, the gearmotor gains a more significant increase in torque relative to conventional motors. Across the entire frequency range, the gearmotor achieves complete coverage of the torque-frequency curve.
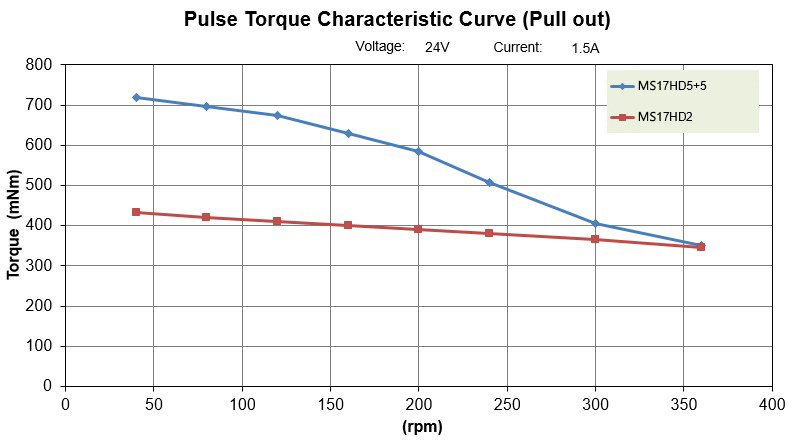
4. Specifications of stepper gearmotor
Below are the specifications of the gearmotors. The MS17HA, MS17HD, and MS17HE series can each be matched with one of three gearboxes, offering ratios of 5, 10, and 25, to suit various torque needs in different working conditions.
Parameters | MS17HA | MS17HD | MS17HE | |||||||
---|---|---|---|---|---|---|---|---|---|---|
Motor parameters | Step Angle(°) | 0.9 | 1.8 | 3.6 | ||||||
Length(mm) | 25.3 | |||||||||
Frame Size(mm) | 42.3 | |||||||||
Holding Torque(Nm) | 0.18 | 0.2 | 0.12 | |||||||
Gearhead parameters | Ratio | 5 | 10 | 25 | 5 | 10 | 25 | 5 | 10 | 25 |
Length(mm) | 14 | 14 | 22 | 14 | 14 | 22 | 14 | 14 | 22 | |
The whole motor parameters | Length(mm) | 39.3 | 39.3 | 47.3 | 39.3 | 39.3 | 47.3 | 39.3 | 39.3 | 47.3 |
Holding Torque(for reference)(Nm) | 0.9 | 1.8 | 4.5 | 1.0 | 2.0 | 5.0 | 0.6 | 1.2 | 3.0 |
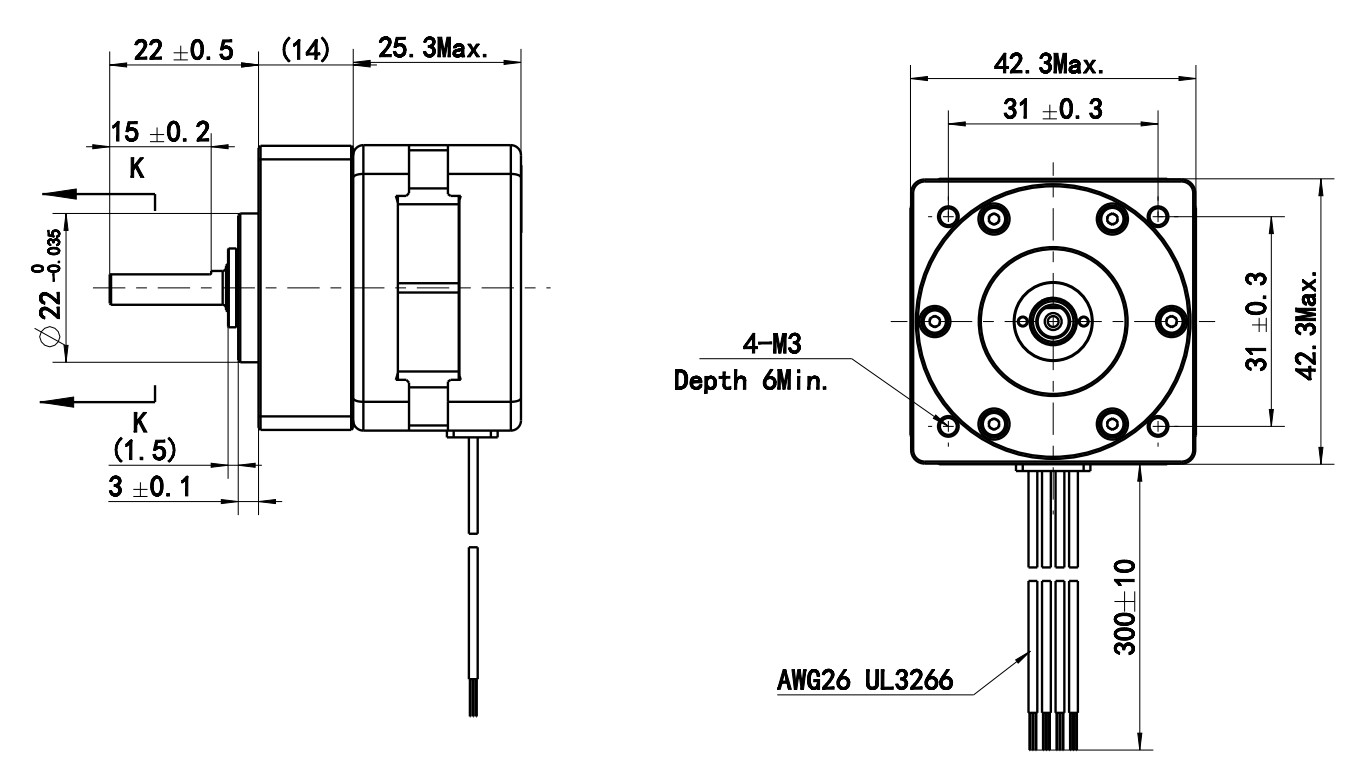