Servo Motors Vs Stepper Motors: Understand Difference
Stepper motors, functioning as open-loop control systems, are fundamentally linked to modern digital control technologies. Currently, stepper motors are extensively utilized within domestic digital control systems. However, with the advent of fully digital AC servo systems, AC servo motors have become increasingly prevalent in these systems. In response to the evolving trends in digital control, most motion control systems now incorporate either stepper motors or fully digital AC servo motors as their driving motors. Despite their similar control mechanisms (pulse and direction signals), there are considerable differences in their performance and application contexts. This text will compare the two in terms of usage performance.
Basic Structure
- Stepper Motor Structure Diagram
- Servo Motor Structure Diagram
1. Different Control Precision
Hybrid stepper motors generally have step angles of 1.8°,0.9° for two-phase models, and 0.72°,0.36° for five-phase models. To achieve even finer precision, some high-performance stepper motors utilize micro stepping. For example, MOONS' manufactures two-phase hybrid stepper motors that pair with their SR series stepper drivers to offer 16 micro stepping subdivisions. These include step angles of 1.8°, 0.9°, 0.45°, 0.36°, 0.225°, 0.18°, 0.1125°, 0.09°, 0.072°, 0.05625°, 0.045°, 0.036°, 0.028125°, 0.018°, 0.0144°, and 0.014°, accommodating both two-phase and five-phase configurations. The precision control of AC servo motors is ensured by a rotary encoder located at the end of the motor shaft. For example, the M2 AC servo motor, which is equipped with a 2500-line incremental encoder and utilizes internal quadrupling technology, achieves a pulse equivalent of 0.036° per 360°/10000. In the case of motors fitted with a 17-bit encoder, the driver processes 131,072 pulses per revolution, equating to a pulse equivalent of 360°/131072=0.0027466°. This value is approximately 1/655 of the pulse equivalent for a stepper motor with a 1.8° step angle, illustrating the superior precision offered by AC servo motors.2. Different characteristics at low frequencies
Stepper motors are prone to low-frequency vibrations when operating at low speeds. These vibrations, whose frequency typically equals half the motor's unloaded resonant frequency, are influenced by load conditions and driver performance. This low-frequency vibration, inherent to the working principles of stepper motors, can significantly hinder the normal functioning of machinery. To mitigate such vibrations at low speeds, damping techniques are essential. These can include installing dampers on the motor or incorporating micro stepping technology in the driver.Anti-Resonance
- A key limitation of stepper motor systems is their inherent resonance points. The SR series stepper drivers address this by automatically calculating these resonance points and adjusting the control algorithms to suppress them. This significantly improves mid-frequency stability, resulting in higher torque output and enhanced high-speed performance.
AC servo motors operate with exceptional smoothness, exhibiting no vibrations even at low speeds. AC servo systems are equipped with resonance suppression features that compensate for any deficiencies in mechanical rigidity. Additionally, these systems include an internal frequency analysis function (FFT), which identifies mechanical resonance points, thereby facilitating system adjustments.
Vibration Suppression
The vibration suppression capabilities of the M2 servo system include two key components: resonance suppression and damping-based vibration reduction.- • Resonance Suppression Function
Two sets of notch filters are employed to effectively address resonance issues that arise from the inherent characteristics of the equipment's mechanical structure. - • Damping Vibration Reduction Function
The damping coefficient provided by the controller is adjustable, which enhances the damping characteristics of the entire motion system and effectively reduces system vibrations.
3. Differences in Torque-Frequency Characteristics
The output torque of a stepper motor decreases with increasing speed and drops sharply at higher speeds, which is why its maximum operating speed is generally between 300 and 600 RPM. Conversely, AC servo motors offer constant torque output; they can deliver their rated torque up to their rated speed, typically 2000 RPM or 3000 RPM, and maintain a constant power output beyond this speed. • Comparison of Speed-Torque Characteristics between Servo Motors and Stepper Motors of the Same Size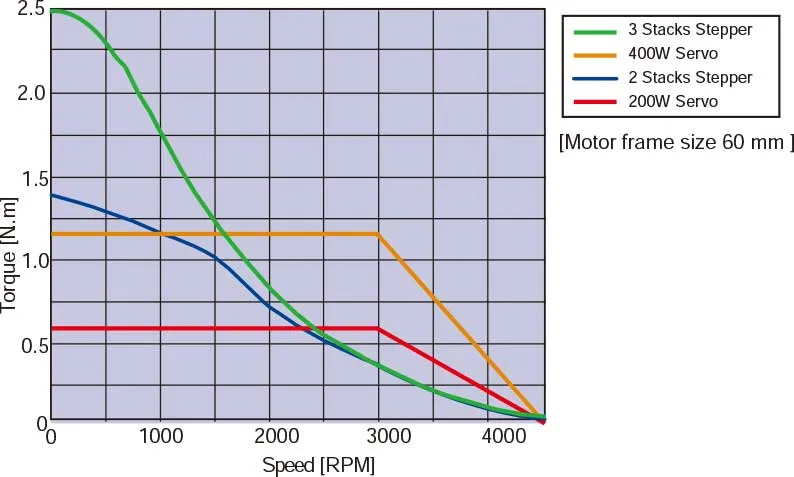